이중 사출 성형
간단한 설명:
이중 사출 성형 두 세트의 금형을 동일한 사출기에 동시에 사출하여 두 개의 서로 다른 플라스틱 재료의 한 부분을 형성하는 플라스틱 성형 공정입니다.
이중 사출 성형 (이중 사출 성형, 2 색 사출이라고도 함).
이중 사출 성형은 두 세트의 금형을 동일한 사출기에 동시에 사출하여 두 개의 서로 다른 플라스틱 재료의 한 부분을 형성하는 플라스틱 성형 공정입니다. 때로는 두 재료의 색상이 다르고 때로는 두 재료가 경도와 부드러움이 다르므로 제품의 필요한 기계적 특성과 미학을 얻습니다.
이중 사출 플라스틱 금형 및 부품의 적용
이중 사출 성형을 통해 생산 된 플라스틱 부품은 전자 제품, 전동 공구, 의료 제품, 가전 제품, 장난감 및 기타 거의 모든 플라스틱 분야에서 널리 사용되었습니다. 이중 색상 금형의 생산 및 성형은 물론 이중 색상 사출 성형기 및 이중 색상 사출 성형 용 원료의 연구 개발도 빠르게 발전했습니다.
이중 사출 부품 사례보기
두 종류의 플라스틱이 사용되며, 두 종류의 플라스틱을 명확히 구분할 수있는 플라스틱 제품을 이중 사출 부품이라고합니다.
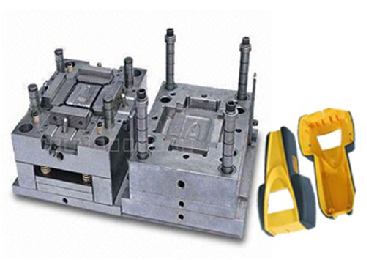
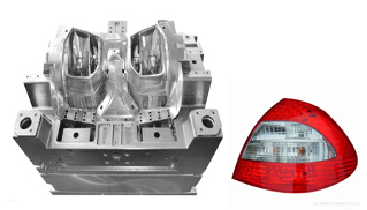
이중 사출 성형의 장점은 무엇입니까?
기존 사출 성형과 비교할 때 이중 재료 동시 사출 성형 공정은 다음과 같은 장점이 있습니다.
1. 부품의 내층과 외층은 내층의 강도가 좋은 소재와 외면의 색상 또는 결이있는 소재 등 특성이 다른 소재를 채택하여 종합적인 성능과 외관 효과를 얻습니다.
2. 재질 소프트-하드 코디네이션 : 부품의 본체는 딱딱한 재질을 사용하며, 탄성 소프트 레진 (TPU, TPE)을 사용하는 어셈블리 매칭 표면은 방수, 방진 등 제품에 아주 좋은 밀봉 효과를 발휘할 수 있습니다.
3. 무거운 부품의 표층은 연질 플라스틱 수지를 사용하는 등 다양한 사용 특성에 따라 부품의 몸체 또는 코어는 경질 플라스틱 수지를 사용하거나 발포 플라스틱은 무게를 줄일 수 있습니다.
4. 낮은 품질의 핵심 재료를 사용하여 비용을 줄일 수 있습니다.
5. 부품의 핵심 재료는 제품 성능을 높이기 위해 안티 전자기 간섭, 높은 전도도 및 기타 재료와 같은 비싸고 특수한 표면 특성을 사용할 수 있습니다.
5. 부품의 표면 또는 코어는 제품 성능을 높이기 위해 전자기 간섭, 높은 전도도 및 기타 재료와 같은 특수한 특성을 가진 고가의 재료로 만들 수 있습니다.
6. 피질과 코어 재료를 적절히 혼합하면 잔류 응력을 줄이고 부품의 기계적 강도 또는 표면 특성을 높일 수 있습니다.
7. 오버 몰딩에 비해 품질, 비용 및 생산성면에서 큰 장점이 있습니다.
이중 사출 성형의 단점
1. 이중 사출 성형기 구매에 투자 할 필요가 있습니다.
2. 이중 사출 금형의 일치에는 정밀도가 필요합니다. 후면 금형의 요구 사항은 동일합니다. 제품에 디자인이 변경되면 두 금형 모두 동일하게 변경해야합니다. 이것은 다이의 유지 관리에 작업 부하를 추가합니다.
3. 이중 사출 성형기는 두 쌍의 금형이 동일한 사출 성형기의 공간과 힘을 공유하므로 대형 제품을 사출 할 수 없습니다.
이중 사출 성형 공정과 오버 몰딩 공정의 차이점
이중 사출 성형과 오버 몰딩은 모두 2 차 사출 성형이지만 상당히 다릅니다.
1. 2 차 성형이라고도하는 오버 몰딩 공정 금형은 일반 사출 성형기에서 수행됩니다. 제품은 두 단계로 구성됩니다. 한 세트의 금형에서 제품을 제거한 후 두 번째 사출 성형을 위해 다른 세트의 금형에 넣습니다. 따라서 오버 몰딩 공정에는 일반 사출 성형기가 사용됩니다.
2. 이중 사출은 두 종류의 플라스틱 재료를 동일한 사출 성형기에 사출하여 두 번 성형하지만 제품은 한 번만 나오는 것입니다. 일반적으로 이러한 종류의 성형 공정은 이중 재료 사출 성형이라고도하며 일반적으로 두 세트의 금형으로 완료되며 특수 이중 사출 성형기가 필요합니다.
3. 이중 사출 성형은 연속 생산 방식입니다. 부품을 꺼내어 중간에 배치하는 작업이 없으며 부품 교체 시간과 오류를 줄이고 생산 불량률을 크게 줄이고 오버 몰딩 공정에 비해 제품 품질과 생산 효율성을 크게 향상시킵니다.
4. 오버 몰딩 공정은 품질 요구 사항이 낮고 주문량이 적은 제품의 사출 성형에 적합합니다. 이중 사출 성형기의 사양에 의해 제한되며 일반적으로 대형 부품의 사출 성형에는 적합하지 않습니다.
5. 이중 사출 금형의 두 전면 금형은 동일해야하며 캡슐화 금형에는이 요구 사항이 없습니다. 따라서 이중 사출 금형의 정밀도와 비용은 캡슐화 된 사출 금형보다 높습니다.
이중 사출 성형 공정의 팁 :
1. 이중 사출 성형 과정에는 이중 사출 성형기, 이중 사출 금형, 적절한 플라스틱 재료 및 합리적인 부품 설계의 네 가지 필수 요소가 있습니다.
2. 연질 및 경질 고무 이중 사출 성형의 재료 선택 2 색 사출 성형을 위해서는 두 종류의 재료의 융점 사이에 일정한 온도 차이가 있어야합니다. 일반적으로 제 1 주사 재의 융점은 제 2 주사 재의 융점보다 높고, 제 1 주사 재의 융점은 제 2 주사 재의 융점보다 높은 것이 권장된다.
3. 투명 및 불투명 재료의 주입 순서 : 첫 번째 샷은 불투명 재료로 만들어지고 두 번째 샷은 투명 재료로 만들어집니다. 예를 들어, 불투명 재료는 일반적으로 재료 온도가 높은 PC이고 두 번째 투명 재료에는 PMMA 또는 PC가 사용됩니다. PC는 UV를 뿌려서 보호해야합니다. PMMA는 UV 또는 경화를 선택할 수 있습니다. 표면에 문자가 있으면 UV를 선택해야합니다.

이중 사출 성형기 란?
두 개의 배럴과 사출 시스템 및 금형의 위치 변환 메커니즘을 갖춘 사출 성형기는 이중 사출 성형기라고하며 이중 색상 사출 성형에 사용됩니다. 사출 성형기는 일반적으로 사출 나사가있는 평행 사출 성형기와 사출 나사가있는 수직 사출 성형기의 두 가지 유형이 있습니다.
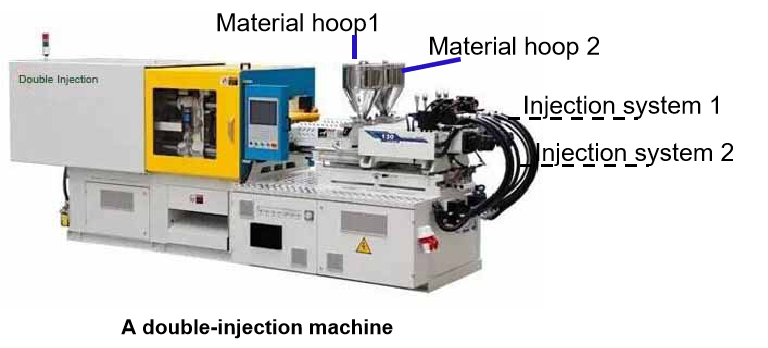
이중 사출 금형이란?
두 종류의 플라스틱을 순차적으로 주입하여 2 색 제품을 생산하는 금형을 2 색 금형이라고합니다. 2 색 사출 금형은 일반적으로 첫 번째 및 두 번째 샷에 해당하는 한 부품에 대한 두 세트의 금형입니다. 두 다이의 후면 다이 (남성 다이)는 동일하지만 전면 다이 (암 다이)는 다릅니다.
이중 사출 금형은 정상적인 생산을 위해 이중 사출 성형기에 설치되어야합니다.
이중 사출 금형 설계 팁
1. 금형 코어 및 캐비티
이중 사출 금형의 성형 부분은 기본적으로 일반 사출 금형과 동일합니다. 차이점은 두 위치에있는 사출 금형의 펀치가 동일한 것으로 간주되어야하고 오목한 금형이 두 펀치와 잘 협력해야한다는 것입니다. 일반적으로 이러한 종류의 플라스틱 부품은 더 작습니다.
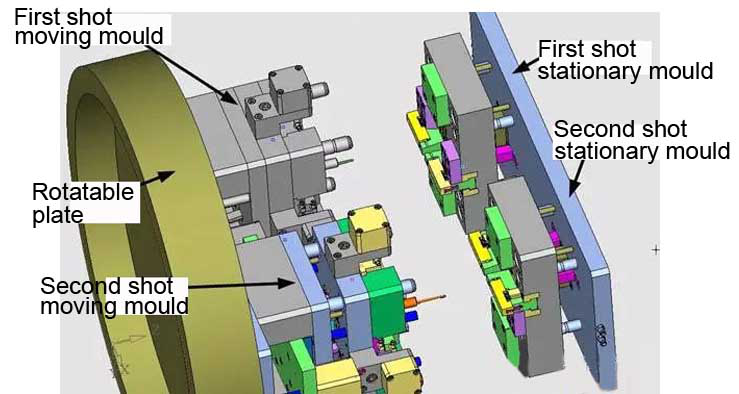
이중 주입 형
2. 배출 메커니즘
2 색 플라스틱 부품은 두 번째 사출 후에 만 탈형 될 수 있으므로 1 차 사출 장치의 탈형 메커니즘이 작동하지 않습니다. 수평 회전 사출기의 경우 사출기의 토출 메커니즘을 사출 토출에 사용할 수 있습니다. 수직 회전 사출기의 경우 사출기의 토출 토출 메커니즘을 사용할 수 없습니다. 유압 토출 토출 토출 토출 메커니즘은 회전 테이블에 설정할 수 있습니다.
3. 게이팅 시스템
이중 사출 성형이기 때문에 게이팅 시스템은 각각 두 개의 사출 성형 장치로 구성된 단일 사출 시스템과 2 차 사출 시스템으로 나뉩니다.
4, 몰드베이스의 일관성 이중 사출 성형 방식이 특별하기 때문에 서로 협력하고 조정해야하므로 두 쌍의 다이 가이드 장치의 크기와 정밀도가 일치해야합니다. 수평 회전 사출 금형의 경우 금형의 닫힘 높이는 동일해야하며 두 금형의 중심은 동일한 회전 반경에 있어야하며 차이는 180이어야합니다. 수직 회전 사출 성형기의 경우 두 쌍의 금형 같은 축에 있어야합니다.
이중 사출 성형 개발
다색 사출 성형과 이중 소재 동시 사출 성형의 특성과 응용을 보면 향후 기존의 사출 성형 공정을 점진적으로 대체하는 경향이 있음을 알 수있다. 혁신적인 사출 성형 기술은 사출 성형 공정의 정밀도를 향상시킬뿐만 아니라 사출 성형 공정 분야를 열어줍니다. 혁신적인 배출 장비 및 프로세스는 다양하고 고품질의 고 부가가치 제품에 대한 증가하는 수요를 충족하기에 충분합니다.
Mestech는 수년간 자동차 케이스, 핸드 헬드 장비 쉘, 스피커 하우징, 키 버튼, 핸들 및 기타 2 색 또는 2 가지 재료 제품에 이중 사출 성형을 제공합니다. 수요가있는 경우 당사에 문의하십시오.